Healthcare management requires several different types of product range of which medical instruments and consumables are very important. These products are typically designed and manufactured in a clean environment to minimize contamination from viable organisms. These products are often intended for procedures or situations where the risk of infection is low.
Common types of non-sterilized medical products include:
Reusable Medical Instruments: Instruments like stethoscopes, blood pressure cuffs and monitors are manufactured in a clean environment.
- Non-Invasive Devices: Items that do not enter sterile areas of the body, such as bandages, splints, and some types of diagnostic equipment.
- Consumable Supplies: Products like cotton balls, gauze, and tongue depressors that are used in a relatively low-risk environment.
- Medical Garments: Items such as non-sterile gloves, gowns, and masks, which are used in non-sterile and non-operating environments.
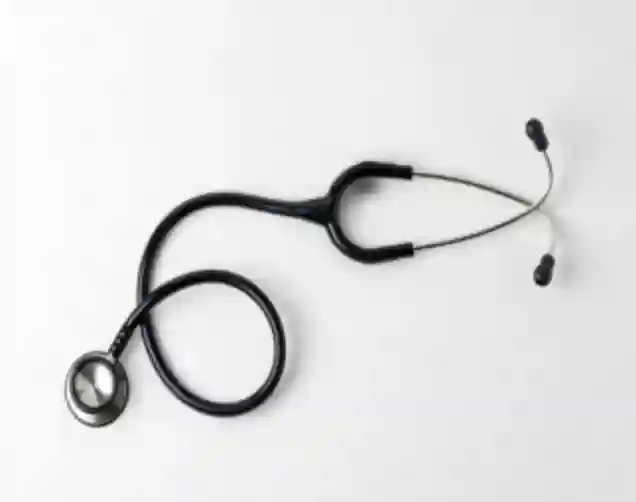
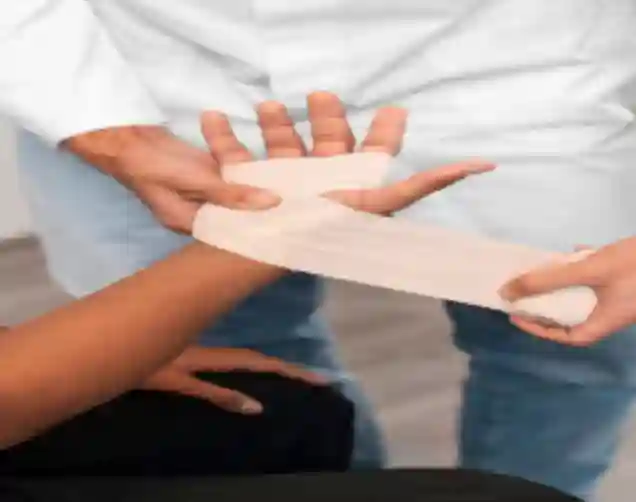
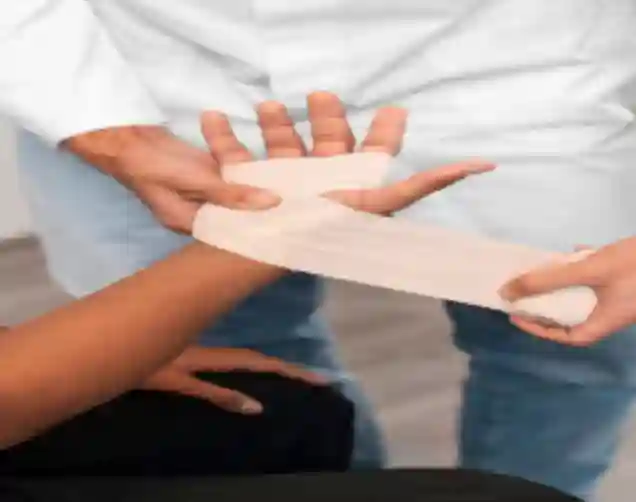
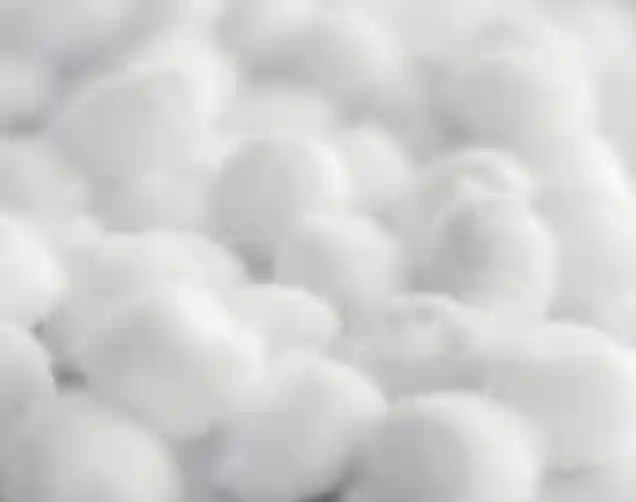
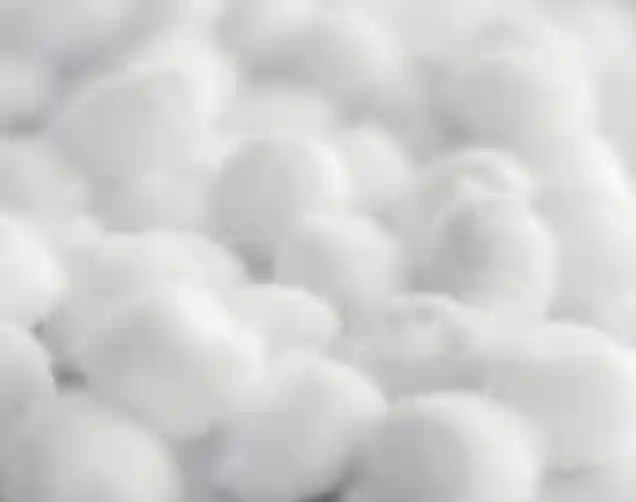
Good Manufacturing Practices (GMP) for non-sterilized medical products are essential to ensure product quality and safety. These practices include stringent controls over the entire manufacturing process, from the sourcing of raw materials to final product packaging. Key elements include maintaining a clean and controlled production environment, implementing robust quality control and quality assurance systems, and ensuring that all equipment and processes are validated and regularly monitored. Medical instruments also need to be manufactured with precision and must provide accurate results. Staff must be adequately trained, and detailed records must be kept tracing all production activities and any deviations. Adherence to GMP minimizes the risk of contamination, defects, and inconsistencies, ensuring that non-sterilized medical products are safe and effective for their intended use.
The use of such medical supplies is also required for Global clinical trials and must be manufactured in a clean environment. Good Manufacturing Practices (GMP) is essential to maintain the integrity and quality of these products. GMP guidelines provide a framework for manufacturing processes that must be rigorously followed during production and supply. This adherence ensures consistency, safety, and efficacy across different regions, facilitating the approval process and market acceptance. By integrating GMP principles, help in identifying potential risks and implementing corrective measures early, thereby enhancing the reliability and success of such non-sterilized medical instruments and consumables on a global scale.
Medical instruments and supplies manufacturers play a crucial role in ensuring the safety and efficacy of non-sterilized medical products by adhering to Good Manufacturing Practices (GMP). These practices, mandated by regulatory agencies, provide guidelines that these manufacturers must follow to maintain high standards of quality throughout the production process. Good Manufacturing Practices (GMP) for non-sterilized medical instruments and consumables offer a range of advantages that ensure product quality, safety, and regulatory compliance.
Here are some of the key benefits:
- Enhanced Product Quality
- Consistency: GMP ensures that products are manufactured consistently, reducing variations and defects.
- Standardization: Uniform production processes lead to standardized product quality, meeting predefined specifications.
- Improved Safety
- Contamination Control: GMP minimizes the risk of contamination by ensuring clean and controlled manufacturing environments.
- Quality Control: Rigorous testing and validation processes detect and prevent defects that could harm users.
- Regulatory Compliance
- Legal Requirements: Adhering to GMP helps companies comply with local and international regulatory requirements, avoiding legal issues and penalties.
- Market Access: Compliance with GMP is often a prerequisite for entering and staying in certain markets, ensuring broader market access.
- Operational Efficiency
- Process Optimization: Standardized procedures streamline manufacturing processes, improving efficiency and reducing waste.
- Cost Savings: Reduced rework, fewer recalls, and optimized resource utilization lower overall production costs.
- Consumer Confidence
- Trust: High-quality, safe products build consumer trust and brand loyalty.
- Reputation: Companies adhering to GMP are viewed more favorably by consumers, healthcare providers, and regulators.
- Risk Management
- Problem Prevention: Proactive quality management systems identify potential issues before they escalate, mitigating risks.
- Crisis Management: Robust traceability and documentation facilitate effective response in case of product issues or recalls.
- Improved Documentation and Traceability
- Record Keeping: Detailed records and documentation ensure traceability and accountability throughout the production process.
- Audit Readiness: Well-maintained records facilitate internal and external audits, demonstrating compliance and quality assurance.
- Employee Training and Engagement
- Skill Development: Regular training ensures that employees are knowledgeable about best practices and standards.
- Motivation: A structured work environment with clear guidelines fosters employee engagement and responsibility.
- Sustainability and Environmental Impact
- Waste Reduction: Efficient processes and quality control reduce waste and environmental footprint.
- Resource Management: GMP promotes better use of resources, supporting sustainable manufacturing practices.
Thus, implementing Good Manufacturing Practices for non-sterilized medical instruments and consumables is crucial for ensuring the quality, safety, and efficacy of medical products. It benefits manufacturers by enhancing operational efficiency, ensuring regulatory compliance, and building consumer trust, while also mitigating risks and supporting sustainable practices.